





Snead, D. R.; Jamison, T. F. Chem. Sci. 2013, 4, 2822, DOI: 10.1039/c3sc50859e
End-to-end continuous flow synthesis and purification of diphenhydramine hydrochloride featuring atom economy, in-line separation, and flow of molten ammonium salts
E-mail: tfj@mit.edu
Tel: +1 617 253-2135
DOI: 10.1039/C3SC50859E, http://pubs.rsc.org/en/content/articlelanding/2013/sc/c3sc50859e#!divAbstract
A continuous end-to-end synthesis and purification of diphenhydramine hydrochloride featuring atom economy and waste minimization is described. Combining a 1:
1 molar ratio of the two starting material streams (chlorodiphenylmethane and N,N-dimethylaminoethanol) in the absence of additional solvent at high temperature gives the target compound directly as a molten salt (ionic liquid above 168 °C) in high yield. This represents the first example of continuous active pharmaceutical ingredient (API) production in this manner. Six of the twelve principles of green chemistry as defined by the American Chemical Society are achieved, most prominently waste minimization and atom economy.
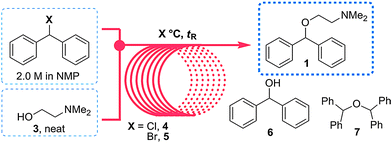
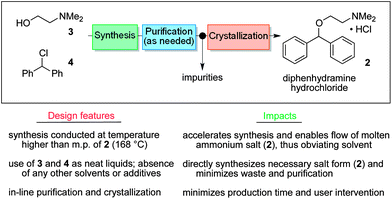
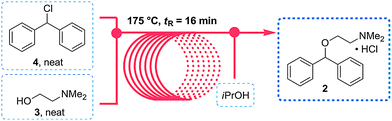
In 2013 the Jamison group reported the flow synthesis of the important H1-antagonist diphenhydramine·HCl (92) showcasing the potential of modern flow chemistry to adhere to green chemistry principles (minimal use of organic solvents, atom economy etc.) . The synthetic strategy relied on reacting chlorodiphenylmethane (93) with an excess of dimethylaminoethanol (94) via a nucleophilic substitution reaction (Scheme ).
As both starting materials are liquid at ambient temperature the use of a solvent could be avoided allowing direct generation of the hydrochloride salt of 92 in a high temperature reactor (175 °C) with a residence time of 16 min. Conveniently at the same reaction temperature the product was produced as a molten paste (m.p. 168 °C) which enabled the continued processing of the crude product circumventing any clogging of the reactor by premature crystallisation. Analysis of the crude extrude product revealed the presence of minor impurities (<10%) even when stoichiometric amounts of 94 were used, consequently an in-line extraction process was developed. Additional streams of aqueous sodium hydroxide (3 M, preheated) and hexane were combined with the crude reaction product followed by passage through a membrane separator. The hexane layer was subsequently collected and treated with hydrochloric acid (5 M in IPA) leading to the precipitation of diphenhydramine hydrochloride (92) in high yield (~90%) and purity (~95%). Furthermore, options to further reduce waste generated during the purification sequence are presented by combining hot IPA with the crude flow stream leading to the isolation of the target compound (92·HCl) by direct crystallisation in the collection vessel (yield 71–84%, purity ~93%, productivity 2.42 g/h).
David Snead
- dsnead at mit dot edu
Ph.D. | The University of Florida, 2010 with Prof. Sukwon Hong |
B.S. | The University of North Carolina at Chapel Hill, 2005 with Prof. Joseph DeSimone |
Timothy F. Jamison
Professor of Chemistry
Massachusetts Institute of Technology
Department of Chemistry
77 Massachusetts Ave., Bldg 18-590
Cambridge, MA 02139
Phone: (617) 253-2135
Fax: (617) 324-0253
Email: tfj at mit dot edu
Curriculum Vitae
IR
MASS
13C NMR
RAMAN