A key pharmaceutical intermediate (1) for production of edivoxetine·HCl was prepared in >99% ee via a continuous Barbier reaction, which improves the greenness of the process relative to a traditional Grignard batch process. The Barbier flow process was run optimally by Eli Lilly and Company in a series of continuous stirred tank reactors (CSTR) where residence times, solventcomposition, stoichiometry, and operations temperature were optimized to produce 12 g h−1crude ketone 6 with 98% ee and 88% in situ yield for 47 hours total flow time. Continuous salt formation and isolation of intermediate 1 from the ketone solution was demonstrated at 89% yield, >99% purity, and 22 g h−1 production rates using MSMPRs in series for 18 hours total flow time. Key benefits to this continuous approach include greater than 30% reduced process mass intensity and magnesium usage relative to a traditional batch process. In addition, the flow process imparts significant process safety benefits for Barbier/Grignard processes including >100× less excess magnesium to quench, >100× less diisobutylaluminum hydride to initiate, and in this system, maximum long-term scale is expected to be 50 L which replaces 4000–6000 L batch reactors.
A continuous flow Barbier reaction was employed for the production of a key pharmaceutical intermediate (1) in the synthesis of edivoxetine·HCl (a highly selective norepinephrine re-uptake inhibitor).
US scientists from Eli Lilly and Company and D&M Continuous Solutions, led by Michael Kopach, report the development of a continuous Barbier reaction which preserves chirality and the product obtained in >99% ee. The team ran the process in a series of continuous stirred tank reactors, where residence time, solvent composition, stoichiometry and operations temperature were optimised to produce 12 g per hour of the ketone precursor to 1 with 98% ee and 88% in situ yield for 47 hours total flow time. Continuous salt formation and isolation of 1 could then be achieved from the ketone solution with >99% purity.
This process offers up several significant advantages over a traditional Grignard batch process. This continuous flow method gave greater than 30% reduced process mass intensity and magnesium usage relative to the batch method. Equally, the flow process resulted in >100 x less excess magnesium to quench and >100 x less diisobutylaluminum hydride to initiate giving significant safety benefits. The authors expect that the maximum long-term scale of the process is 50 L which would replace 4000-6000 L batch reactors.
Continuous Flow Barbier Reaction
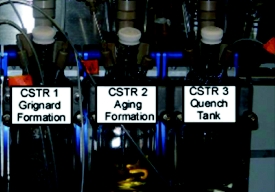
For 100 years, Grignard reactions have been one of the most powerful and effi cient organic chemistry methodologies for C-C bond formation. However, Grignard reactions are also among the most challenging reactions from both operational and potential safety issues due to initiation diffi culties and runaway potential. A close variation to the Grignard reaction is the Barbier reaction wherein the Grignard reagent is prepared in the presence of an electrophile resulting in the immediate consumption of the Grignard. A Barbier reaction using a CSTR was developed for a key pharmaceutical intermediate in production of edivoxetine·HCl (Scheme 4) [9]. In the fl ow setup (Figure 2), solid magnesium is sequestered in the fi rst tank where the Grignard initiation event takes place. CSTR 2 was used as an aging tank and CSTR 3 was the quench tank. CSTRs were used for Grignard reaction rather than a PFDR because of the solid Mg reagent.

Continuous reaction improved process safety, product quality, and process greenness. The continuous reaction achieved >99% ee in situ versus 95% ee batch because of immediate conversion of unstable intermediate. Solvent volumes were reduced 30%. The safety hazards were reduced by decreasing the reactor size by 50X, which reduced chemical potential and also increased heat transfer surface area per unit volume by 4X. DIBAL-H initiating agent was reduced by more than 100X, and excess Mg that must be quenched at the end of reaction was almost eliminated. When run continuously, the commercial scale Grignard formation reactor was expected to be 50L, which replaces 4000-6000L batch reactor.
The continuous flow Barbier reaction: an improved environmental alternative to the Grignard reaction?
E-mail: kopach_michael@lilly.com
DOI: 10.1039/C2GC35050E
http://pubs.rsc.org/en/Content/ArticleLanding/2012/GC/C2GC35050E#!divAbstract
Three vessel Grignard CSTR process train.
Grignard synthesis of compound 1.
Retrosynthesis of edivoxetine·HCl.
Flow diagram for the whole continuous process from amide 3 to product 1.
Continuous crystallization of compound 1.
Distillation and continuous crystallization of compound 1.
Entry, Rxn temp. (°C), Vol. ratio THF–toluene (%), Conversion (%), ee (%)
//////////The continuous flow, Barbier reaction, improved environmental alternative, Grignard reaction, FLOW SYNTHESIS
Sorry, the comment form is closed at this time.